Abaqus Co-Simulation: Thermal Coupling
This tutorial demonstrates how to run a thermal co-simulation case using Simcenter STAR-CCM+ and Abaqus. Co-simulation involves a strong coupling between the two codes, in which data exchange occurs at frequent intervals, that are known as coupling steps. In this case, data is exchanged at the end of each time-step, and a relatively large time-step is used to approximate a steady-state solution.
The deep level of communication between the solvers allows you to obtain a full solution across the solid-fluid interface. The solution includes the effects of the interaction between the solid and fluid domains. Simcenter STAR-CCM+ passes heat flux data to Abaqus, and Abaqus passes temperatures back to Simcenter STAR-CCM+. In each case, the thermal data defines a boundary condition in the model, to be used in the next set of iterations.
The coupling is carried out using the SIMULIA Co-Simulation Engine, which exchanges data between the two models automatically during the co-simulation. This technique differs from the file-based method in that the coupling between the two codes is much stronger; the exchange of data is carried out automatically, and Simcenter STAR-CCM+ and Abaqus run simultaneously.
To prepare a co-simulation case, two models are required. The Abaqus model is for the solid domain, and is used to create an Abaqus input file. In Simcenter STAR-CCM+ the fluid model is set up, with the appropriate boundary conditions defined. For each model, specify a set of co-simulation parameters which define the boundary/surface at the fluid-structure interface, the field functions that are imported and exported at this interface, the frequency of coupling steps, and so on. With the co-simulation parameters defined, Abaqus can be launched from the Simcenter STAR-CCM+ GUI, and the co-simulation run.
Before running the co-simulation, it is good practice to run standalone cases for the fluid and solid models to make sure that they converge independently. In this example, the Abaqus model could be run standalone using a surface film condition, *SFILM, on the INNER surface with estimated constant values for the sink temperature and film coefficient. Similarly, in Simcenter STAR-CCM+, the simulation could be run using an estimated temperature on the Fluid-Wall boundary.
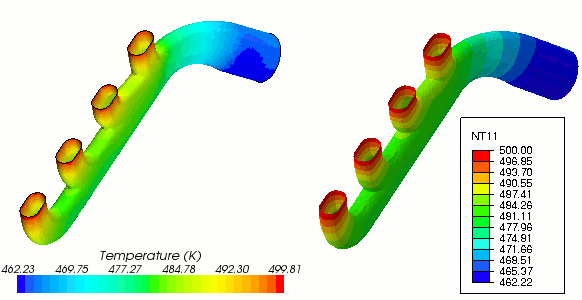
This tutorial is divided into three sections. In the first section, the Abaqus model and input file are created using Abaqus/CAE. In the second section, the fluid model is prepared in Simcenter STAR-CCM+. The third section involves editing the Abaqus input file for co-simulation using a script editor, defining the co-simulation session in Simcenter STAR-CCM+, and running the co-simulation. The third section also demonstrates how to start and close Abaqus via the Simcenter STAR-CCM+ user interface.