Abaqus File-Based Coupling: Exhaust Manifold
The purpose of this tutorial is to demonstrate the typical workflow in running a thermal fluid-structure interaction case using the file-based coupling method with Abaqus.
In the file-based coupling method, the thermal conduction in the solid structure is computed using Abaqus and the two separate simulations in Abaqus and Simcenter STAR-CCM+ are coupled by exchanging data for the fluid-structure interface using files on the hard drive.
Simcenter STAR-CCM+ passes local heat transfer coefficients and reference temperatures to Abaqus and Abaqus supplies the wall temperature to Simcenter STAR-CCM+. In Abaqus terminology, the heat transfer coefficient is referred to as film coefficient and the reference temperature is referred to as sink temperature. The goal is to exchange data between the two codes for enough times so that you reach a converged solution. This can be accomplished using the GUI by manually performing the import-map-export operations, and launching Abaqus runs after each exchange of data. It is also possible to carry out the Simcenter STAR-CCM+ steps automatically by using Java macros, which is demonstrated in this tutorial.
The case is an exhaust manifold subject to 10 m/s inlet gases at 500K. The objective is to find the steady-state solution for the flow and temperature in the exhaust gas, and the temperature in the solid manifold. Abaqus leads the process by providing the initial steady-state solution for the wall-temperature on the interior surface of the manifold, based on estimations for the thermal conditions in the manifold. From the initial Abaqus solution, Simcenter STAR-CCM+ extracts the wall temperatures, map them onto the fluid model, and use them to set a boundary condition for the energy equation in the fluid region. From the Simcenter STAR-CCM+ solution, the local heat transfer coefficients and reference temperatures are mapped and exported to Abaqus, and in the next iteration Abaqus uses this data to obtain a set of wall temperature data. These data exchanges are repeated until the wall temperatures, heat transfer coefficients, and reference temperatures have converged.
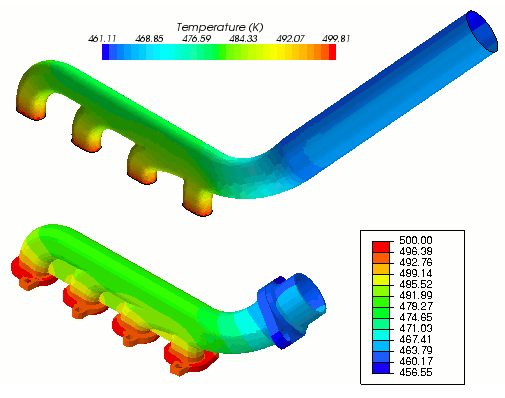
This type of coupling algorithm is referred to as a loose coupling algorithm, that is, where files on the hard disk are used to exchange data. Simcenter STAR-CCM+ supports this method of coupling by allowing users to generate output files in a number of different formats that can be read by third-party software. In this tutorial, the heat transfer coefficients and reference temperatures are exported to a text file that can be read into Abaqus. This text file uses the keyword *FILM to specify the type of field data within the file. More information on the *FILM keyword can be found in the Abaqus Keywords Reference Manual.
An input file for the Abaqus analysis has been provided for this tutorial, which contains the manifold geometry and the settings required for the Abaqus job. A surface mesh for the fluid in the manifold has also been prepared for the tutorial; this is provided in .dbs format.
Note | You could also use the conjugate heat transfer capabilities within Simcenter STAR-CCM+ to solve the solid manifold temperatures. The setup for such a case is demonstrated in the Thermal Strain: Exhaust Manifold tutorial. |