Abaqus Co-Simulation: Mechanical Coupling
This tutorial demonstrates how to carry out a mechanical co-simulation case using Simcenter STAR-CCM+ and Abaqus. Co-simulation involves a strong coupling between the two codes. Data is exchanged at frequent intervals that are called coupling steps. This level of communication between the solvers allows you to obtain a full solution across the fluid-solid interface.
In a mechanical coupling, Simcenter STAR-CCM+ passes traction loads to Abaqus (pressure + wall shear stress), and Abaqus passes displacements to Simcenter STAR-CCM+. In Abaqus, the traction loads are applied to the surface of the solid structure. In Simcenter STAR-CCM+, the displacements are used as an input to the mesh morpher.
During the co-simulation, data is automatically exchanged between Simcenter STAR-CCM+ and Abaqus using the SIMULIA Co-Simulation Engine. This technique differs from the file-based method in that the coupling between the codes is much stronger, and Simcenter STAR-CCM+ and Abaqus run simultaneously.
To set up a co-simulation case, separate models must be prepared for the fluid and the solid domains. The solid model is set up in Abaqus, and defined within an Abaqus input file. The fluid model is set up in a Simcenter STAR-CCM+ simulation where the appropriate boundary conditions and physics are defined. For each model, a set of co-simulation parameters must be specified. The parameters identify the boundaries/surfaces that make up the fluid-structure interface, the field data that is imported/exported at the interface, the frequency of coupling steps, and so on. Simcenter STAR-CCM+ is used to run the co-simulation when the setup is complete.
Before running the co-simulation, it is good practice to run standalone cases for the fluid and solid models to make sure that they converge independently. In this example, the Abaqus model could be run standalone using an applied pressure load, *DSLOAD, on the plate surface with an estimated constant value for the pressure. The Simcenter STAR-CCM+ simulation could be run without mesh morphing, using a fixed plate.
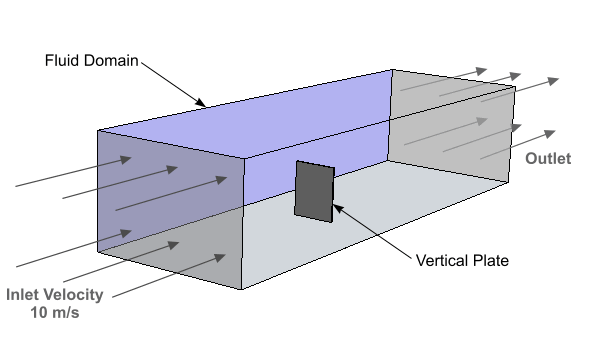
In this tutorial, the fluid domain is initialized by running a quasi-steady simulation. The initial flow field is then used as the initial condition for the co-simulation. Once the initial flow field is established, the solver settings are changed to the values that are required for the co-simulation. When the co-simulation is run, the plate is released and bends in the wind. In the tutorial, the co-simulation is run for 0.125s, which is about half the fundamental period of the first bending mode and about 2.5 vortex shedding periods. Running the case for longer (around 4 s) shows that the first bending mode is damped, and the first twisting mode dominates plate motion.