Electroplating
Electroplating is a technique that is commonly used in industry to deposit a metal coating on parts. The part that requires coating sits within an electrolytic solution that contains metal ions. A current is then induced through the electrolyte, between the part acting as the cathode, and an anode that is made of the same metal as the metal ions. In this tutorial, you simulate electroplating of a plastic grille part, which is pre-coated with copper and nickel, using chromium ions.
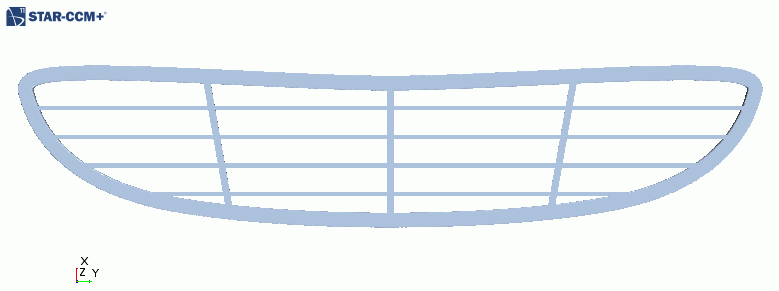
In this tutorial, a voltage difference is applied between a chromium anode and a cathode that is formed from a plastic grille that already has a coating of copper and nickel. The voltage difference drives positively charged chromium ions (Cr3+) through the electrolyte from the anode to the cathode. When the Cr3+ ions reach the surface of the cathode, they gain electrons from the cathode and form chromium atoms. Since the metal chromium atoms are insoluble, they remain on the surface of the cathode to form a thin plate layer. As electrons move through the circuit from the anode to the cathode, metal chromium atoms at the anode lose electrons and become chromium ions in solution.
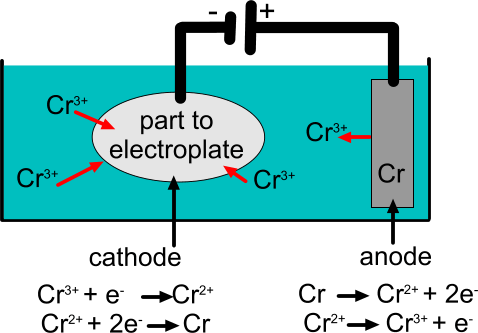
In this tutorial, the plastic grille part is held in the electrolyte solution by a metal rack which conducts electrons from the circuit to the grille part. The plastic grille is already coated with thin layers of copper and three types of nickel. The metal rack is coated in paint to prevent it becoming plated, although it is exposed near each point of contact with the grille. The conductivity of the metal rack is much greater than the conductivity of the electrolyte or the previously plated material. Therefore, ohmic losses are negligible and the electric potential in the rack is considered to be constant. A constant electric potential boundary condition is defined at the contact points between the rack and the grille.
Since the electrolyte solution is water-based, and hydrogen ions are reduced more easily than chromium ions, passing an electric current through the solution also creates hydrogen gas at the cathode surface.
This unwanted side reaction consumes part of the electric current. In this tutorial, the detailed reaction mechanism is not modeled. Instead, the aggregate polarization curve is imported from a table [997], and a Faraday efficiency factor accounts for the fraction of current that is associated with the metal deposition reaction.
- current density vector
- electrical conductivity
- electric potential
equilibrium potential at zero current
is a non-linear function which the Butler-Volmer, Tafel, or Tabular Polarization Curve describe.
The current density at the interface represents the total current for all electrochemical reactions at the surface. Side reactions, such as the evolution of hydrogen gas, result in a decrease in efficiency. Therefore, the efficiency of the surface mechanism that is used represents the amount of current which goes towards the plating reaction. This mechanism is based on the current densities that are calculated at the cathode, according to Song and Chin [997], at electric potentials that are relative to the standard hydrogen electrode (SHE).
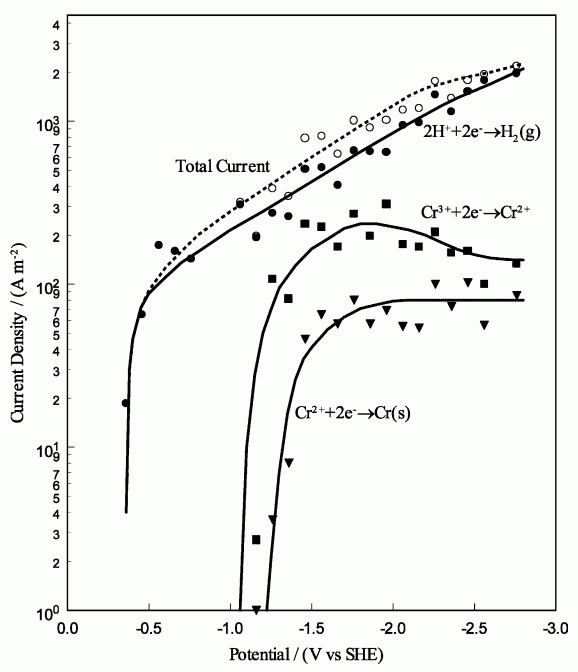
Depending on the reason for electroplating parts, the thickness of the metal coating can become significant. If the coating is intended to protect the part from corrosion, then a thicker coating is required than if the coating is for decorative purposes. In this tutorial, the thickness of the pre-coated layer is approximated as the constant thickness of the shell region that represents the coating. To model a more accurate representation, you can run a transient simulation which accounts for the changing thickness at each time-step.
- is the plating thickness [m]
- is the molecular mass of the metal plating, which in this case is 51.99 for chromium [kg/kmol]
- is the charge of metal ion, which in this case is 3.
- is the Faraday constant, which is 96,485,336.5 [s A/kmol].
- is the plated metal mass density, which in this case is [kg/m³]
- is the plating time, which in this case is 300 [s]
- is the current density (Boundary Specific Electric Current) which is returned from the simulation by a field function [A / m²]
- is the plating efficiency. The Song_Cr3+Polarization table contains lists of plating efficiencies at various current densities. This data is interpolated to return plating efficiencies at the local values of current density (Boundary Specific Electric Current).
When running the tutorial, the thickness of the chromium coating and the electric potential of the cathode (grille) are monitored using scalar scenes. If the current at the cathode drops, the rate of electrodeposition of chromium also drops. Therefore, you also plot the electric current at the anode and the cathode.