Sponge Layer Modeling: Simplified Tailpipe
Unsteady aeroacoustics simulations require effective non-reflective boundary conditions to prevent spurious reflected acoustic waves from the boundaries of the computational domain interfering with the aeroacoustic results.
Simcenter STAR-CCM+ provides the Sponge Layer model, which achieves non-reflective conditions at the boundaries by damping the flow field unsteadiness within a zone of specified thickness—the sponge layer. This damping prevents the acoustic waves and vortical disturbances from reaching the boundaries and eliminates spurious back-reflected waves.
The focus of this tutorial is on demonstrating how to set up an unsteady compressible direct noise aeroacoustic simulation using Large Eddy Simulation (LES) for predicting turbulence and the Sponge Layer model for providing non-reflective conditions near the outlet boundary.
You simulate the jet flow from a simplified tailpipe expanding into the environment. The following diagram shows the configuration of the pipe geometry and the boundaries:
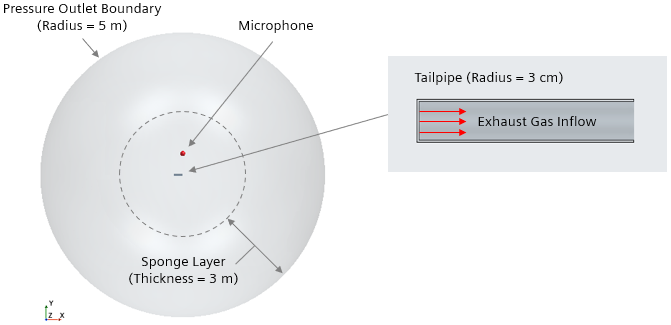
The compressible gas, here modeled as air using the ideal gas law, enters the duct with a mass flow rate of 0.15 kg/s and a total temperature of 700 K. The gas leaves the open pipe and expands into the environment, which creates unsteady flow structures and acoustic effects. The environment is bounded by a spherically shaped pressure outlet with an atmospheric pressure of 101325 Pa and a temperature of 300 K. The unsteady flow structures and sound propagate towards the pressure boundary, which requires a sponge layer at the boundary to ensure that the pressure waves pass through it without reflection. You resolve acoustic waves up to a frequency of 500 Hz.
After the simulation is complete, you perform spectral analyses of the time signals received at a microphone above the tailpipe. You compare the results with provided data from the same simulation without using a sponge layer.