Acoustic Modal Analysis: Thermo-Acoustic Stability of a Cylindrical Burner
Thermo-acoustic instability, that is, large-amplitude pressure oscillations, can be encountered in many devices such as gas turbines, rocket engines, or combustors. The instabilities, which can have detrimental consequences, are excited by the feedback loop between the unsteady combustion and the natural acoustic modes of the devices.
Depending on the results of a steady-state compressible flow simulation, the Acoustic Modal Analysis model computes the acoustic frequencies, normalized mode shapes, and their linear growth rates within the geometry. As part of the Acoustic Modal Analysis model, Simcenter STAR-CCM+ provides the N-Tau model, which describes the flame transfer function that accounts for the effect of unsteady heat release fluctuations on the acoustic pressure.
This tutorial demonstrates the workflow for setting up an acoustic modal analysis to investigate the thermo-acoustic stability of a combustion device. In this tutorial, you simulate the combustion of propane (C3H8) in a cylindrical burner.
The following schematic diagram shows the configuration:
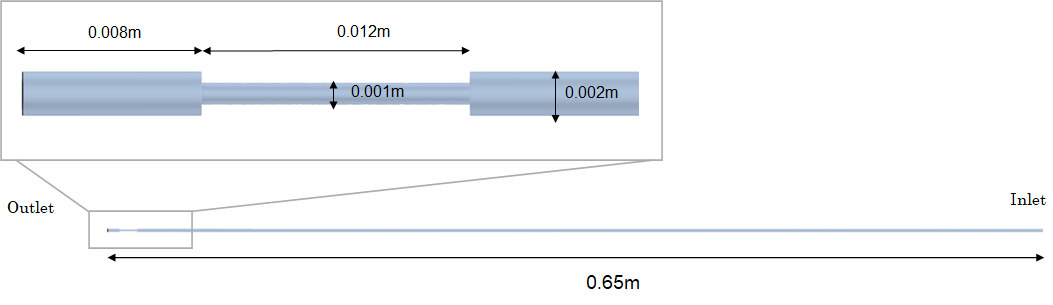
You run the tutorial simulation in two steps:
- You perform a steady-state flow with combustion simulation to be used as basis
for the acoustic modal analysis.
At the inlet boundary, propane, oxygen, and nitrogen, here modeled as a multi-component gas mixture, enter the burner with a velocity of 0.15 m/s. At the outflow boundary, you impose a pressure value of 0 Pa. Combustion is ignited between iterations 200 and 300 using a pulsed temperature ignitor. The chemical reaction is modeled by the Eddy Break-Up model.
- You perform the acoustic modal analysis on the previously obtained converged
solution.
You use the Acoustic Modal Analysis model to compute the acoustic frequencies, normalized mode shapes, and linear growth rates. For this burner simulation, it is expected that the 5th and 6th predicted modes are unstable. Therefore, you set the number of nodes to 6 to capture these modes. You use the N-Tau model to describe the flame transfer function and specify the reference location and time delay properties for the burner.
As a result, the acoustic frequencies and linear growth rates are reported to identify the positive growth rates and corresponding unstable modes. Acoustic mode shapes and frequencies are used to illustrate that the mode shapes are longitudinal within the cylindrical burner geometry.