Reacting Channels: Steam Methane Reforming
In this tutorial, you use the Reacting Channel Coupling co-simulation model in Simcenter STAR-CCM+ to solve a reacting flow simulation using the same method as is required for systems such as: reformers, crackers, and process heaters.
There are two domains that are required in the geometry—the reacting channels (the tubes in which the processes occur) and the surrounding firebox.
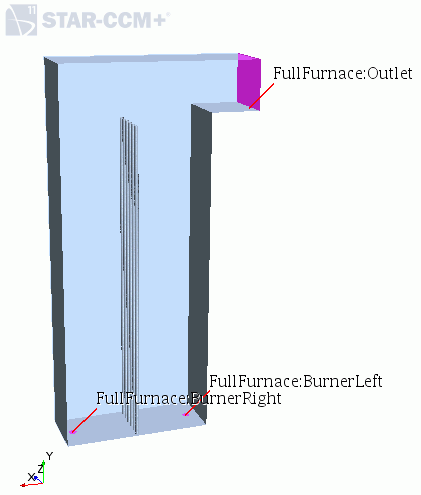
The firebox is modeled as a three-dimensional calculation in Simcenter STAR-CCM+. The physics for the 1D processes in the reacting channels is modeled as a 1D plug flow reactor using the CVODE solver within the same Simcenter STAR-CCM+ simulation. The co-simulation capability allows the exchange of information between the 3D firebox and the 1D process calculations in the reacting channels, and also enforces the energy balance in the system. In the co-simulation, the information that is exchanged is the net heat flux of the reacting channels and the outer reacting channel wall temperatures. Additionally, detailed information on scalar and velocity profiles on the firebox and tubes is also available during the simulation.
1D modeling of the reacting channel physics is a computationally efficient alternative to 3D modeling of all reacting channels in the system. Especially if there are hundreds of tubes in industrial scale geometries. The geometry that is used in this tutorial consists of a simplified representation of a firebox that involves two burners with six reacting channels in-between the burners. Each burner has the same fuel composition and flow rate; the six tubes are the same length, diameter, and have the same properties. Exhaust gases from three of the reacting channels re-enter the remaining three reacting channels.
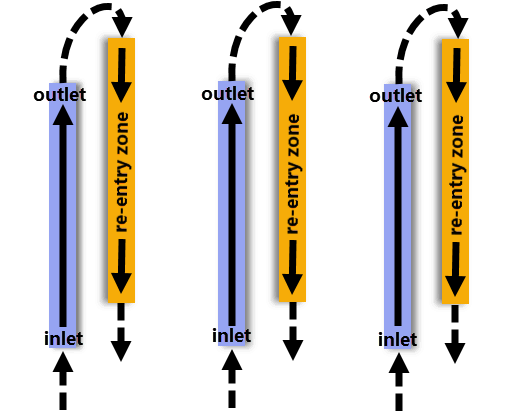
The objective of this tutorial is to set up the firebox and the physics for the reacting channels, and to evaluate the scalar profiles on the firebox and reacting channels.
The starting file for this tutorial contains pre-defined region and boundary settings. The mesh settings that are used are adequate to demonstrate the set-up, and obtain qualitative results from the simulation of reacting channels. For simulations that require more quantitative results, use finer mesh settings.
In the firebox, a partially premixed mixture of methane, air, and trace amounts of hydrogen is burned to generate high temperatures for heating the reacting channels. The flamelet generated manifold (FGM) model is used with the chemical mechanism, GRI-Mech 3.0 [990].
In the reacting channels, Steam-Methane Reforming (SMR) reactions are simulated using a plug flow reactor (PFR) library—compiled for Windows or Linux. Methane and steam enter the reacting channels which contain a catalyst, and during the reformation process, carbon monoxide and hydrogen are produced. The gaseous mixture of carbon monoxide and hydrogen is referred to as synthesis gas, which is an important feedstock in the production of many other chemicals, in particular ammonia and methanol. Since the reformation process is endothermic, the reacting channels are required to be heated to high temperatures to provide sufficient energy. To account for the presence of a catalyst inside the reacting channels, the reactions are modeled in a packed bed system.