Flamelet Generated Manifold: Perfectly Premixed Combustion with Adaptive Meshing
This tutorial simulates lean perfectly-premixed propane combustion using the Flamelet Generated Manifold (FGM) model in a combustor where the flame is stabilized behind a V-shaped bluff body. The Large Eddy Simulation (LES) model is used to directly resolve the large scales of the turbulence, and model the small scale motions, in the flow domain.
To reduce the computational cost of combustion simulations, Simcenter STAR-CCM+ provides adaptive mesh refinement (AMR), which uses reacting flow specific criteria—error indicators based on progress variable, mixture fraction, or temperature—to refine or coarsen the mesh only where needed while the simulation is running. This approach eliminates the need to estimate the position of the flame upfront to be able to refine the mesh appropriately before the simulation starts.
The FGM model parameterizes all of the species in a detailed chemical mechanism by mixture fraction, reaction progress, and enthalpy—calculated a-priori from simulations in a simple 0D reactor or 1D premixed flame. The effects of detailed chemistry on combustion are stored in an FGM table which you generate in Simcenter STAR-CCM+.
You specify which species the FGM table stores, and the required values are retrieved during the CFD simulation. In this tutorial, the flame is ignited by initializing to a burnt composition everywhere. However, it is possible to use the progress variable ignitor with the FGM model instead.
This tutorial demonstrates how to set up a large eddy simulation with an adaptive mesh, while avoiding computational cost for the purpose of demonstration. A 3D hexahedral mesh is used that is only a few cells thick—almost 2D. It is not possible to use the Adaptive Mesh model with a true 2D mesh, and the LES model is strictly applicable to 3D geometries. This (almost) 2D LES is not predictive and is only used here to reduce run-time.
The solution is run for a maximum physical time which allows for three flow-through cycles—industrial simulations would typically require more flow-throughs to collect sufficient statistics.
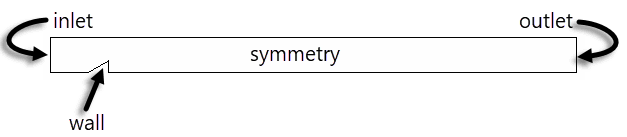
- Dynamic viscosity: 1.716E-5 Pa-s
- Molecular diffusivity: Determined using the Schmidt Number
- Specific heat: Determined from values in the FGM table
- Thermal conductivity: Determined using a constant Lewis Number
At the inlet, the premixed fuel mixture (by mass: 3.69% C3H8, 22.15% O2, and 74.16% N2) enters the combustor at a temperature of 600 K, and pressure of 1 atmosphere. The velocity at the inlet is 29.0 m/s in the X direction and 0.0 m/s in the Y direction.