Multiphase flow is a term which refers to the flow and interaction of
several phases within the same system where distinct interfaces exist between the phases.
Simcenter STAR-CCM+ considers flow options where phases coexist
as: gas bubbles in liquid, liquid droplets in gas, and/or solid particles in gas or liquid,
and/or (large scale) free surface flows.
The term ‘phase’ usually refers to the
thermodynamic state of the matter: solid, liquid, or gas. In modeling terms, a phase is
defined in broader terms, and can be defined as a quantity of matter within a system
that has its own physical properties to distinguish it from other phases within the
system. For example:
- Liquids of different density
- Bubbles of different size
- Solid granules of different
size and/or weight
Multiphase flows are different from
multi-component flows. In multi-component flows, the different species are mixed at the
molecular level. These species have the same convection velocity. In multiphase flows,
the different phases are mixed at the macroscopic scale. These phases have different
convection velocity. Many flows are multiphase multi-component flows.
Multiphase flows can be classified into
two categories:
- Dispersed flows, such as
bubbly, droplet, and particle flows
- Stratified flows, such as free
surface flows, or annular film flow in pipes.
A phase is considered dispersed if it
occupies disconnected regions of space—otherwise it is continuous.
Simcenter STAR-CCM+
provides the following distinct multiphase models to meet the requirements of the two
main categories of flow:
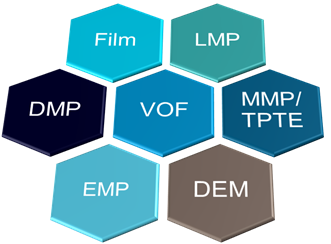
Model |
Key
Applications |
Example
Applications |
- Dispersed Multiphase (DMP)
-
Simulates flows of low loadings of particles
dispersed in a continuous phase (dilute multiphase
mixture) in a Eulerian manner. Provides a
lightweight alternative to the Lagrangian Multiphase
model. The conservation equations for mass,
momentum, and energy are solved for each dispersed
phase. The transport equations of the continuous
phase are solved by a single phase model.
The
DMP model is suitable for dispersed flows of
droplets, bubbles, and solid particles with low
volume fraction of the dispersed phase.
|
- Automotive Soiling
- Aerospace Icing
- Wet steam in low pressure steam turbine
stages
|
|
- Eulerian Multiphase (EMP)
- This
model, based on the concept of interpenetrating
continua, solves conservation equations for mass,
momentum, and energy for each phase. The phases share
the pressure field and the inter-phase interactions need
to be modeled to close the set of equations. Phase
interaction models are provided to define the influence
that one phase exerts upon another across the
interfacial area between them. The EMP model is used to
model the dispersed flows of bubbles, droplets, solid
particles, and for modeling a combination of dispersed
and stratified flows.
|
- Bubble Columns
- Mixing Vessels
- Settling Tanks
- Fluidized Beds
- Multiphase Separators
-
Stepped
Spillway
-
Multiphase
Pumps
-
Phase
Change equipments
|
|
- Fluid Film
- Predicts
the dynamic characteristics of wall films using boundary
layer approximations and assumed velocity and
temperature profiles across the depth of the film. Film
transport is predicted using thin shells that lie across
the surface of solid walls on which the film is formed.
- The Fluid
Film model is suitable for stratified thin liquid film
flows over surfaces.
|
- Vehicle Rainwater Management
- Selective Catalytic Reduction (SCR)
- Fuel Sprays
- Lubrication
- Spray Coating/Deposition
- Aircraft Ice Protection
|
|
- Mixture Multiphase (MMP)
- A
simplified multiphase model that can be used to model
the flow of miscible phases. In this model, the
computational efforts are reduced by assuming the
multiphase mixture to be a homogeneous single-phase
system for which only one set of transport equations is
solved.
- The MMP
model is suitable for dispersed flows of mixtures of
bubbles in liquid or droplets in gas.
|
- Partially resolved gearbox/tank sloshing
- Multiphase pumps
- Fuel Cells
- Boilers
- Steam generators
|
|
- Two-Phase Thermodynamic Equilibrium
-
A
simplified multiphase mixture implementation, which
is designed for applications that involve two phases
of the same substance, typically water and steam,
which are in thermodynamic equilibrium.
The
Two-Phase Thermodynamic Equilibrium model is
suitable for dispersed flows of two thermodynamic
phases of the same material.
|
- Steam Generators
- Boilers
- Steam Turbines
|
|
- Volume Of Fluid (VOF) Multiphase
-
Provided for systems containing two or more
immiscible fluid phases, where each phase
constitutes a large structure within the system
(such as typical free surface flows). This approach
captures the movement of the interface between the
fluid phases, and is often used for marine
applications.
The
VOF model is suitable for stratified flows (free
surfaces).
|
- Marine Hydrodynamics and Seakeeping
- Fuel Tank Sloshing
- Oil and Gas Flow Assurance
- IC Engine Cooling
|
|
- Discrete Element Method (DEM)
-
This
model is an extension of the Lagrangian framework.
Individual particles are modeled rather than
representative parcels and inter-particle contact
forces are explicitly accounted for. DEM is used to
model densely packed granular flows where particle
shape and collision behavior are important.
The
DEM model is suitable for dispersed flows of
discrete solid particles with high volume fraction
of the particles.
|
- Fluidized beds
- Rock mechanics
- Conveying aggregates
- Tablet coating
- Plugging fissures in oil wells
- Crop harvesting and lawn mowing
|
|
- Smoothed-Particle Hydrodynamics
(SPH)
-
SPH is a numerical method that
overcomes meshing-related constraints occurring with
mesh-based models, while still being based on the
Navier-Stokes equations.
Due to its Lagrangian characteristic and particle
approach, the SPH method can model a wide range of
applications involving dynamic flows with complex
interfaces.
SPH is particularly well-suited for
fast dynamic flows and complex boundaries, including
interfaces with fragmentations and reconnections
such breaking waves, jets and splashes, and moving
parts.
|
- Powertrain lubrication with oil bath
- Sloshing
|
|
- Lagrangian Multiphase (LMP)
-
Solves
the equation of motion for representative parcels of
the dispersed phase as they pass through the system.
For the continuous phase, the conservation equations
for mass, momentum, and energy are solved. It is
intended for systems that consist mainly of a single
continuous phase carrying a relatively small volume
of solid discrete particles, droplets, or bubbles.
It is suited where the interaction of the discrete
phase with physical boundaries is important.
The
LMP model is suitable for dispersed flows of
discrete particles (bubbles, droplets, solid
particles) with low volume fraction of the
particles.
|
- Vehicle Water Management
- Cyclone Separation
- Erosion
- Aerosol Dispersion
- Liquid Fuel Combustion
- Spray Cooling
- Spray Coating
|
|
Simcenter STAR-CCM+
provides a selection of multiphase and phase interaction models to simulate a wide range
of multi-regime and multi-scale multiphase flows. In addition, hybrid modeling can be
used to model multiple flow regimes of a phase material by using a combination of
several different multiphase models.
A common framework has also been developed
to specify the models that define how pairs of phases interact with each other. These
models are known as phase interactions.
The multiphase models can also be used with the
complementary technologies available in Simcenter STAR-CCM+, such
as the population balance modeling to predict the size distribution of the dispersed
phase, adaptive mesh refinement (AMR) for providing a solution-refined mesh, and
adaptive time-stepping for automatic time-step adjustments.