Discrete Element Method (DEM)
The Discrete Element Method (DEM) is an engineering numerical method to simulate motion of many interacting discrete objects that are typically solid particles. Although DEM modeling demands significant computing power, it provides detailed resolution that other methods cannot achieve. In Simcenter STAR-CCM+, DEM can be applied to regions with or without a volume mesh.
Established by Cundall and Strack [94], the DEM model is an extension of the Lagrangian modeling methodology to include dense particle flows. The distinct characteristic of DEM is that inter-particle contact forces are included in the equations of motion. These forces cannot be ignored for highly loaded flows, that is, many interacting particles.
Simcenter STAR-CCM+ uses a classical mechanics method to model DEM, and is based on soft-particle formulation where particles are allowed to develop an overlap. The calculated contact force is proportional to the overlap, as well as to the particle material and geometric properties.
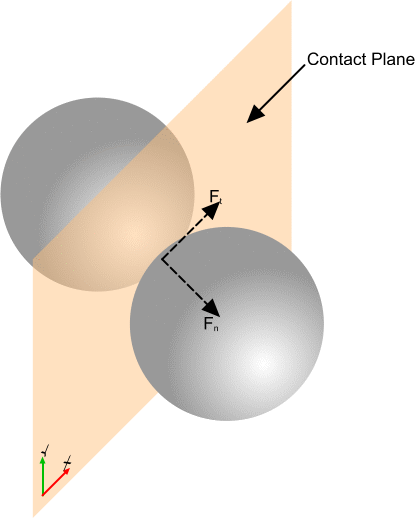
Applications include modeling the granular flow of:
- Sand
- Food particles
- Powders
- Capsules
- Slurries
DEM in Simcenter STAR-CCM+ is implemented within the Lagrangian framework and uses Lagrangian phase models to define the particles. In addition, the DEM model uses its own phase and phase interaction models for specific DEM particle properties and their behavior during contact with each other or wall boundaries.
The DEM model also uses Lagrangian injectors and its own lattice injector and random injector to introduce particles into the fluid region.
After running the solver, you can clear DEM particles from the region by activating the Lagrangian DEM Solution Fields option in the Clear Solution dialog.
Considerations for the Discrete Element Method
When setting up a simulation that uses DEM, take the following points into consideration:
- Use a coarser mesh than typical CFD applications. If a particle is in a small cell and occupies most of its volume, it can cause high void fractions and thus solver instability.
- Use a meshfree region when DEM particles are not significantly affected by the fluid phase and DEM-CFD coupling is not required. See Meshfree DEM Model Reference.
- When using mesh motion, use smaller solver time-steps to improve quality of interpolation for mesh vertex positions.
- Typically, the most robust approach to solving the continuous phase with DEM is to use the coupled solver with incompressible, ideal gas.
- To reduce computation times, reduce the Young’s Modulus of the particles. However, this change in physical properties compromise the accuracy and validity of your results.
Controlling the DEM Time-Step
By default, the duration of the Rayleigh wave (Eqn. (3244)) across the surface of the sphere limits the DEM time-step. Furthermore, a minimum of 10 time-steps are necessary in order to resolve particle collisions correctly (Eqn. (3246)). The distance traveled by particles within a single time-step is constrained (Eqn. (3247)) to account for contact among particles and between particles and walls.
To account for the particle movements with precision, Simcenter STAR-CCM+ uses substeps to assess physics such as flow and gravity (if applicable) as well as DEM. This results in dynamic time-step calculations by default.
To control the time-step, you can control the dynamic calculations of the solver in one of two ways:
- Change the Time Scale property to reduce the allowed fraction of the Rayleigh wave limit.
- Alternatively, enter the
desired time-step in the Static Timestep property. This
causes Simcenter STAR-CCM+ to use the value of
the time-step that you enter. Do not make this option your first choice, as it
can cause a failure to converge.
To restore dynamic calculations, simply enter the default value of 0.0 in this property.