Airgap Remeshing: Electronic Speedometer
Electric machine simulations require a conformal mesh at the interfaces between different components. Airgap remeshing is a meshing technique that allows you to generate and maintain conformal meshes between regions that are in relative motion.
In this simulation, you model a simple device that consists of a magnet and a pair of coils. The magnet has prescribed rotation motion, whereas the coils are fixed. As the motion of the magnet induces a voltage in the excitation coils, the coils act as a sensor to the motion of the magnet and can be used to measure the rate at which the magnet rotates. Electronic speedometers are based on this simple model.
The geometry for this tutorial consists of several parts that represent the magnet, the coils, and the surrounding environment (air). To keep the mesh conformal at the sliding interface, the air domain is divided into multiple portions of which only two are remeshed during each time-step. These two portions are thin and each represents one side of the interface between the moving zones. The other parts of the air domain do not require remeshing. As the problem is symmetric, you only model a 45 degree sector of the geometry and use periodic interfaces.
This tutorial demonstrates a general meshing strategy for electric machine simulations. Complex parts are meshed using a tetrahedral volume mesher. The surface mesh from this complex portion is then extruded into portions of the mesh that have regular shapes. As the geometry in the tutorial is simple, the approach is not strictly necessary here.
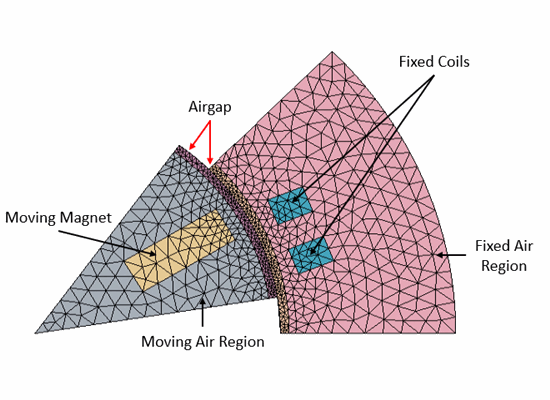