FSI Remeshing and Tessellated Geometry Parts Contact: Rubber Sleeve
Simcenter STAR-CCM+ allows you to model the mechanical contact between a deformable structure and the tessellated surfaces of geometry parts within the simulation. This is useful to simulate the interaction between an elastic solid and a rigid obstacle, without modeling the obstacle explicitly.
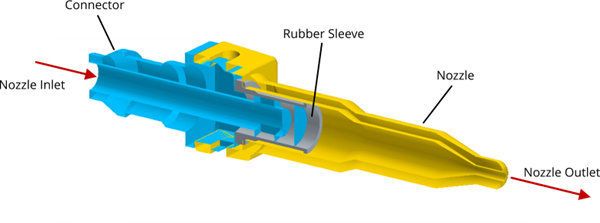
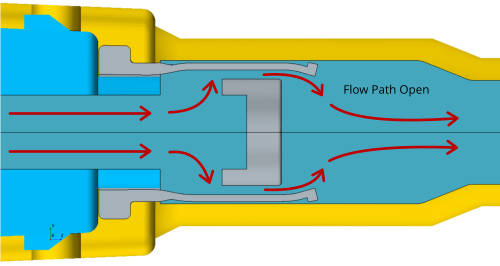
When simulating large deformations, the mesh quality may deteriorate due to the morphing motion. In the nozzle, the deformation of the sleeve leads to a reduced mesh quality in the fluid region. In order to obtain a desirable mesh after deforming the geometry, you remesh the fluid domain.
Due to the concentric design of the cleaning nozzle, you only model a quarter of the nozzle geometry to reduce the cell count and run-time. Additionally, you assume that the deformation can be modelled with a one-way coupled approach, where you model the effects of the solid deformation on the fluid while neglecting the effect of the fluid on the solid.