Fluid-Structure Interaction: Vibrating Pipe
This tutorial demonstrates how to set up fluid-structure interaction (FSI) problems in Simcenter STAR-CCM+.
In this simulation, you study the dynamic vibration of a titanium pipe conveying water. As the mass of the pipe is small compared to the mass of the fluid, the physics of the fluid and the structure is coupled. In the first part of the simulation, you apply a body load to the pipe and run a static/steady analysis to seek the static equilibrium solution, obtaining an initial displacement for the pipe. In the second part of the simulation, you remove the body load and run a dynamic analysis, allowing the pipe to vibrate in real time.
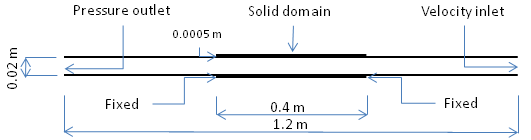
Solid Domain | Fluid Domain | |
---|---|---|
Geometry | Inner diameter: 0.02 m | Diameter: 0.02 m |
Outer diameter: 0.021 m | Length: 1.20 m | |
Length: 0.40 m |
Pipe-contact: only the middle section of the fluid domain is in contact with the pipe |
|
Symmetry: The problem is symmetric about the yz plane, allowing you to model 1/2 of the geometry. | Symmetry: The problem is symmetric about the yz plane, allowing you to model 1/2 of the geometry. | |
Assumptions and Models |
|
|
|
||
Boundary Conditions |
|
|
Type of Analysis | Quasi-static (first run) + Dynamic (second run) | Steady (first run) + Transient (second run) |
Discretization and Solution Method | Finite Element (FE) | Finite Volume (FV) |
Mesh | Hex8 Elements | Hexahedral Cells |