Hyperelastic Stress Analysis with Adaptive Time-Step: Trileaflet Heart Valve
Trileaflet valves are prosthetic heart valves that open and close because of the deformation of the flexible leaflets [993]. Obtaining a successful simulation of the valve opening event is challenging due to the snap through instability on which the valve operation depends. Simcenter STAR-CCM+ provides a dynamic time-step control that makes a successful simulation possible.
In this tutorial, you model the deformation of a trileaflet heart valve as it opens under the influence of pressure. The valve leaflets are constructed from a isotropic hyperelastic polymer which deforms non-linearly under the presence of a load. In this simulation, a Neo-Hookean hyperelastic material law is applied.
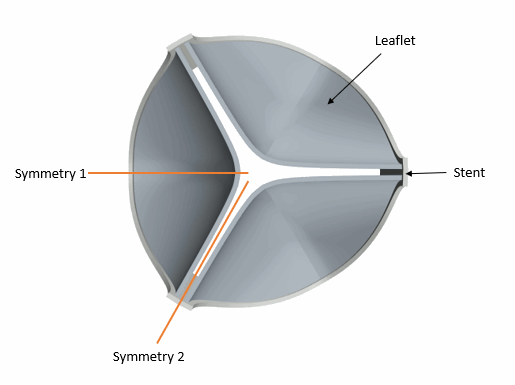
For this case the transient pressure load is defined over a period of 0.861 s, using a table, which represents a full pressure cycle. For half a cycle, representing the opening of the valve, the pressure ranges from a maximum value of 1177 Pa to a minimum value of -14719 Pa [995]. Constraints are applied on the leaflet that fix the leaflets in place and account for the planes of symmetry. To accurately model the snap through instabilities that occur during the operation of the valve the adaptive time-step model is enabled to ensure that the time-step is optimized with respect to a change in displacement of half the leaflet thickness.