FSI with Opening and Closing Flow Paths: Diaphragm Valve
Simcenter STAR-CCM+ provides the capability of performing a two-way coupled fluid-structure interaction (FSI) simulation with opening and closing flow paths, which are due to the deformation of a hyperelastic non-linear material such as rubber. This capability can aid in the design of (but is not limited to) seals, valves, and gaskets used within a range of industries.
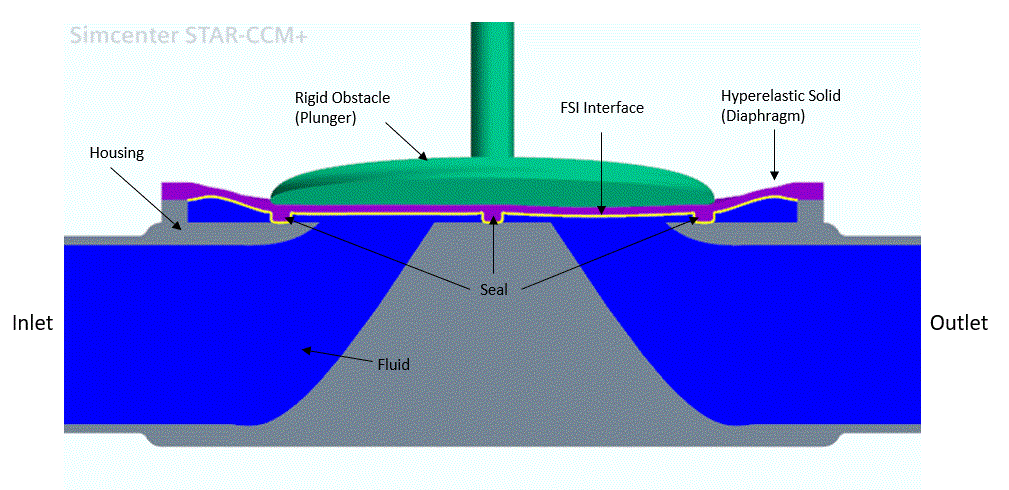
For this specific case an unsteady turbulent flow enters the passage at 0.1m/s from the inlet. The flow passes beneath the rubber diaphragm and pushes against the valve at the FSI interface. Over a period of 4 seconds the plunger moves downwards, causing the diaphragm to deform and close the flow passage between the valve and the housing. The plunger motion is defined by a translation motion in the negative z axis.
The model is split into three regions. The fluid region contains the inlet and outlet for the air flowing through the valve as well as the bypass and the gap boundary between the seal and the structure. A fluid overset region contains the volume of fluid around the deforming seal. The third region, for the solid, contains the diaphragm. To ensure that the flow path can be closed completely, an overset mesh zero gap interface is defined between the fluid region and the fluid overset region.
Two-way coupling is activated in order to model the effect of the diaphragm deformation on the flow, and to account for the impact of the flow on the diaphragm. In the coupling, the displacement field is passed from the solid to the fluid, and the fluid traction (pressure and wall shear stress) is passed from the fluid to the solid. The diaphragm itself is modeled using a hyperelastic material law and is constrained at the rim of the seal.