Adjoint Shape Optimization: Surface Mesh Morphing for Y-Junction Manifold
Simcenter STAR-CCM+ provides the adjoint solution for shape optimization as a method for finding modified designs to improve performance and efficiency.
An adjoint shape optimization uses surface sensitivities to derive an optimized shape with respect to the user-defined cost functions. Surface sensitivies define how the surface is displaced, and control the deformation calculated by the morpher. The optimized position of the surface is to maximize/minimize the cost function of interest.
This tutorial focuses on demonstrating the workflow for setting up a shape optimization study where the deformation of the Y-Junction of a manifold is accounted for by morphing the surface mesh. The Morph Surface Mesh operation allows you to deform the entire part or individual part surfaces of the geometry and to re-run the volume mesh after every optimization cycle. This is particularly beneficial to avoid a bad quality mesh when dealing with large displacements.
The simplified manifold geometry shown in the diagram below, contains an inlet duct, a Y-Junction connection, and two outlet ducts. Air enters the manifold inlet duct with a velocity of 1 m/s and leaves through the two pressure outlet boundaries at atmospheric pressure.
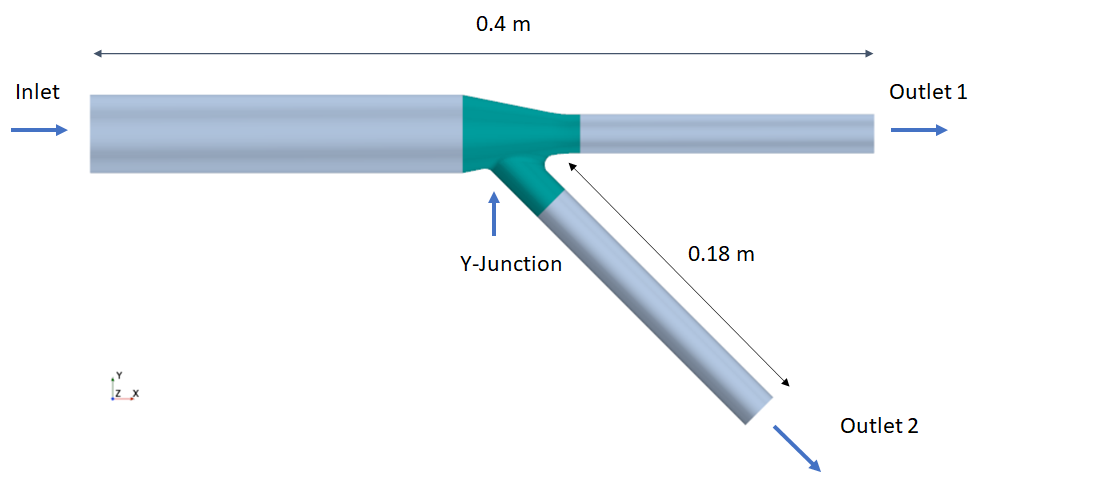
During the simulation operation sequence, the primal flow is solved, followed by the adjoint solver, and mesh deformation. The Morph Surface Mesh operation is used to deform the Y-Junction to a new shape, dictated by the adjoint sensitivities, and defined in the simulation via an imposed displacement vector. The imposed displacement field uses a displacement multiplier parameter to limit the size of the mesh deformation, and is updated with each optimization cycle. Additionally, to ensure a smooth shape optimization, you apply a surface sensitivity filter to the Y-Junction boundary.
The final results demonstrate how the deformation of the Y-Junction allows you to achieve a balanced mass flow split between the manifold two outlets within 5 optimization cycles.