Surrogate FMU: Flapper Valve Representation within Simcenter Amesim
When a 1D fluid system simulation contains a complex hydraulic component, an FMU built from a surrogate model can represent the influence of the component without requiring a full 1D/3D co-simulation. Design Manager provides a facility for exporting such FMUs based on a surrogate model.
In this tutorial, a dual pump transmission system is simulated in Simcenter Amesim. A mechanical oil pump (MOP) works in conjunction with an electrical auxiliary oil pump (EAOP). When the mechanical oil pump is switched off, a flapper valve protects the auxiliary oil pump from damage caused by back pressure. To understand the impact of the valve dynamics on the transmission system, 3D simulation is required for the flapper valve.
The following picture illustrates the original transmission circuit of the dual pump system including the 1D flapper valve component:
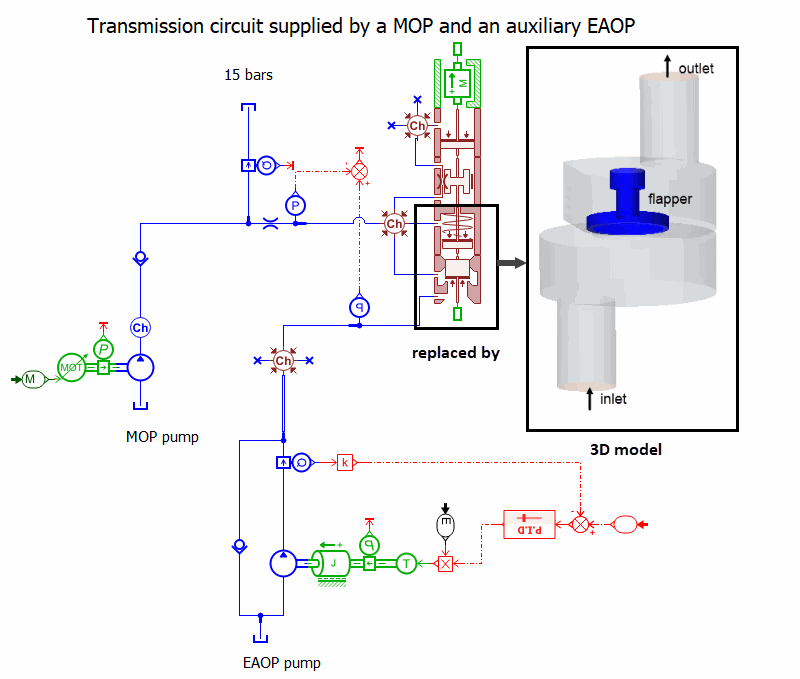
The classic method to link a 1D and a 3D simulation is to set up a co-simulation by exchanging physical variables between the two systems. However, 3D simulations are often time-consuming and require additional licenses. Whenever the operating conditions of the 1D simulation vary, the entire co-simulation must be repeated.
To solve this issue, in Design Manager you can compute a surrogate approximation for each output variable in response to changing inputs. This approach is implemented here for the flapper valve. You export the computed surrogates as an Functional Mockup Unit (FMU) from Simcenter STAR-CCM+. The FMU is imported into Simcenter Amesim as a sub-model that provide an adequate approximation of the 3D flapper valve behavior.
Generally speaking, the surrogate approach is efficient when 3D results can be accurately captured through surrogate approximations. For certain applications, surrogates may not be sufficiently accurate to replace co-simulations.