Blade Element Method: Helicopter Rotor-Fuselage Interaction
The rotating main rotor blades of a helicopter generate a complex flow field that leads to periodic aerodynamic loads on the airframe. Because of these aerodynamic loads, the passenger cabin can be subject to noise and vibration. These aerodynamic interactions affect the performance of helicopters and they can cause structural damage. Simcenter STAR-CCM+ provides a method for simulating the flow generated by rotor blades that does not require you to mesh the blades individually. This method allows you to predict the complex flow field around a helicopter taking into account the fuselage and rotor flow field interaction.
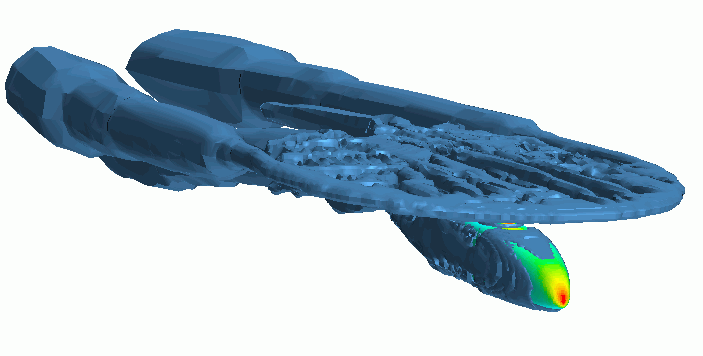
This tutorial simulates the flight of a generic helicopter fuselage using a virtual wind tunnel in Simcenter STAR-CCM+. The ROBIN (ROtor Body INteraction) configuration is used for the airframe where the geometry and operating condition are taken from [982]. The parameter values correspond to Table 17 in this paper.
- Rotation rate:
- Advance ratio:
- Rotor thrust coefficient:
- Rotor shaft angle (pitch angle):
- Collective pitch angle:
- Lateral cyclic pitch angle:
- Longitudinal cyclic pitch angle:
where is the rotor solidity, is the free-stream density, is the rotor thrust, is the rotor disk area, and is the tip speed due to rotation.
To model the helicopter flight, the ROBIN body is positioned within a virtual wind tunnel. In the tutorial, you apply the blade element method of the virtual disk model to simulate the effect of the rotor on the helicopter fuselage. The advantage of the blade element method is that it does not require you to explicitly resolve the rotor blades geometry with a fine mesh. For more information, see Blade Element method in the User Guide.