Turbomachinery Mesh
Turbomachinery applications with axial blades typically require a flow-aligned, structured mesh. This type of mesh has implicit connectivity and a fixed number of vertex or face neighbors, leading to a more accurate solution.
Typically a structured mesh has a lower cell count whilst allowing for the same solution accuracy and since the connectivity is implicit the solver is much more efficient.
The operation supports axial blade geometries, which can include a tip clearance near the hub or shroud that is, a gap between the blade tip and the hub or the shroud. If present, the tip gap clearance can be either constant or variable.
The Turbomachinery Mesh operation generates a flow-aligned hexahedral mesh using a method based on elliptical partial differential equations.
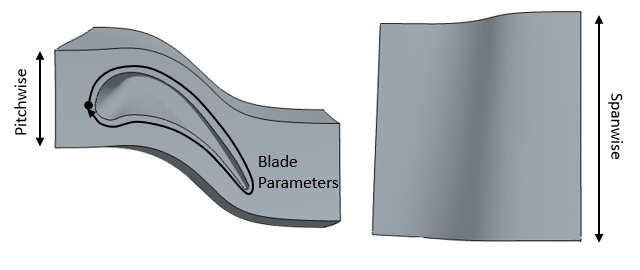