Dual Stream Heat Exchanger: Car Radiator
Heat exchangers are devices that efficiently transfer heat from one medium to another. Some prominent examples of heat exchanger applications include car radiators, such as the one used in this tutorial, power plants and air-conditioning.
The purpose of this tutorial is to demonstrate the workflow for setting up a dual stream heat exchanger simulation in Simcenter STAR-CCM+.
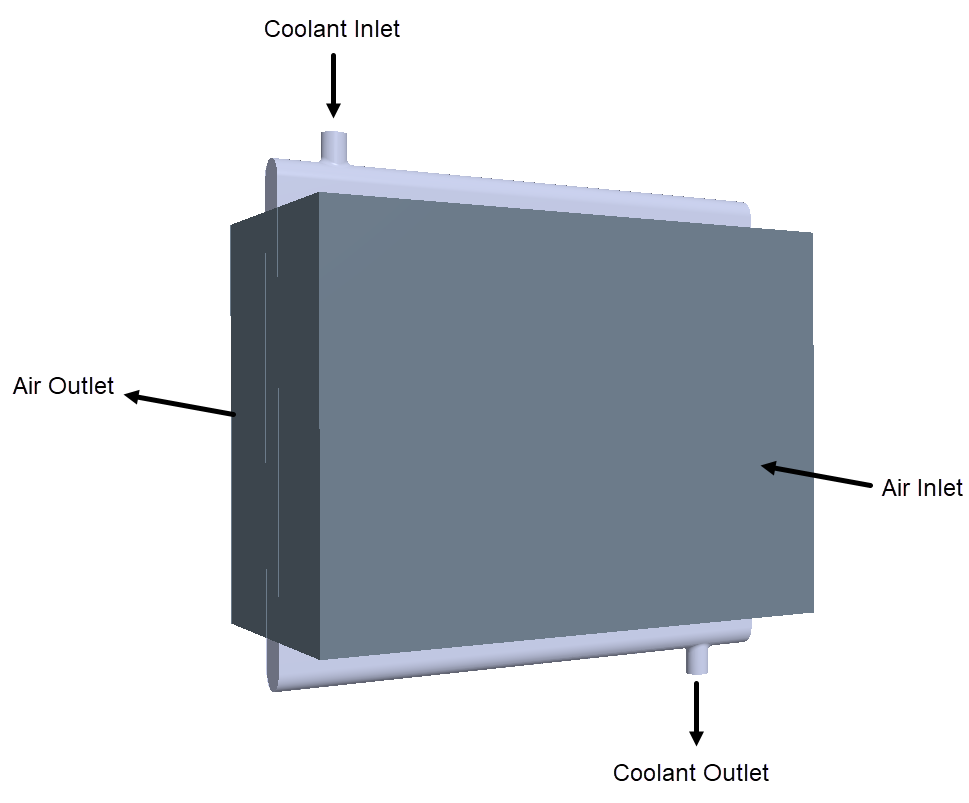
The air stream enters the heat exchanger via the air inlet with a velocity of 20 m/s and a temperature of 35 °C. The coolant stream enters the heat exchanger via the coolant inlet at a mass flow rate of 1.8 kg/s and a temperature of 107 °C.
To model the heat transfer from the coolant stream to the air stream, you use the actual flow dual stream heat exchanger optiion. This heat exchanger option models the addition or removal of heat as a source/sink term to the energy equation of each fluid stream. This approach requires you to create two identical overlapping heat exchanger core regions, one for each stream. To facilitate the heat exchange between the two regions, you create a heat exchanger interface between them. The heat exchanger rate is determined by a UAG table that provides the overall heat transfer coefficient of the heat exchanger as a function of the mass flow rate of air.