Replacing VOF Phases
In some VOF simulations, under-resolution of the mesh, time-step, or other numerical issues can cause numerical ventilation to occur. The VOF Phase Replacement model lets you reduce or eliminate numerical ventilation by replacing the unwanted phase (typically gas) with the appropriate phase (typically liquid) in specified regions. If appropriate, you can specify a maximum volume fraction in the phase replacement.
Ventilation and Numerical Ventilation
Ventilation in marine applications is the entrainment of air under the hull of a vessel. Numerical ventilation is where this phenomenon occurs erroneously in a simulation due to under-resolution of the mesh, time-step or other numerical issues.
An example is shown below: the entire wetted hull surface is covered by an air layer that has a thickness of approximately 0.3 of the first cell layer height. As air has a lower viscosity than water, the simulation results would show a reduced drag on the hull.
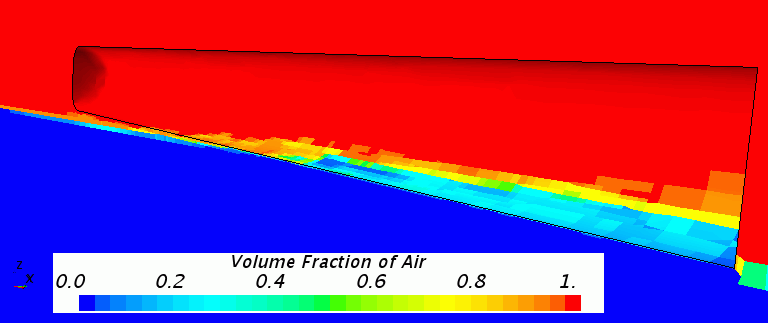
Ventilation is not common in casting applications, but numerical ventilation can occur in a simulation and can have significant effects on the results. For example, in a mold filling simulation, an air layer of one cell thickness isolates the hot melt from the cold mold. This isolation severely affects the heat transfer from the melt to the mold, and therefore affects the solidification time and the occurrence of cold shuts.
An example is shown below: a counter-gravity casting process where the melt flows upstream through a vertical channel has entrained air below the melt surface level. This air layer strongly affects boundary heat transfer.
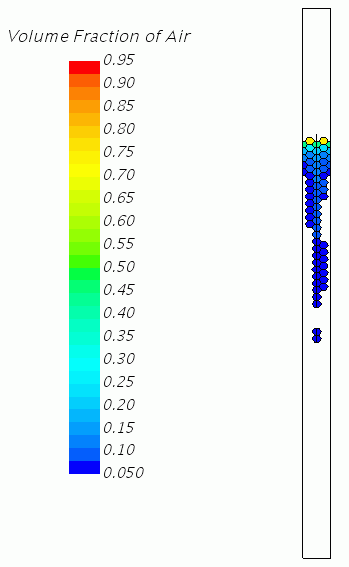
Using the VOF Phase Replacement Model
The VOF Phase Replacement model lets you specify a limit for every cell (the Phase Replacement Volume Fraction Limit) up to which to replace the unwanted gas phase with the appropriate liquid phase. The VOF Phase Replacement model can also be used to eliminate very thin liquid phases from a wall in gas bulk flow simulations (such as external aero applications).
If appropriate, you can specify a maximum volume fraction in the phase replacement. When you activate the VOF Phase Replacement model, the Phase Volumetric Replacement Volume Fraction Limit of <phase> field function becomes available.
This model cannot distinguish between real ventilation and numerical ventilation in a simulation. The model attempts to eliminate a specified VOF phase, replacing it with another specified VOF phase, when the layer thickness decreases below a specified threshold.
The phase replacement is not implemented with source terms to transport equations; instead, some fields are overwritten before the first transport equation is solved within each iteration. For each cell, the VOF Phase Replacement model executes the following actions before all the old variables are updated:
- If the value of the Phase Replacement Volume Fraction Limit is non-zero, the volume fraction of the primary phase is added to the secondary phase up to the limit specified for that cell by the Phase Replacement Volume Fraction Limit.
- The mixture density is updated to match the new volume fraction field.
- The total enthalpy is updated for the primary phase and the secondary phase as well as for the mixture.
This process is important; otherwise the phase replacement would result in contributions to unsteady terms.
The VOF Phase Replacement model is incompatible with the following:
- 2nd order discretization in time