Running the Simulation
To reduce the run time, you only run the simulation for one full rotation of the rotor. This means running for 360 time-steps. In industry, it is typical to run over a large number of revolutions to ensure you obtain a converged result.
- Select the Enabled. node and set Morph From Zero to
To improve accuracy, decrease the tolerance for mesh
morphing:
- Select the 1.0E-10. and set Morpher Tolerance to
-
Select the
node and set the following properties:
Porperty Time-Step ${Xperiod}/${Xsteps_per_rev} Temporal Discretization 2nd-order - Select the Maximum Steps to 360. set
-
Click
(Initialize Solution) in the toolbar.
Initializing the solution triggers Simcenter STAR-CCM+ to read through the input files and import the beam mesh. -
To run the solution, click
(Run).
- When the simulation has finished running, save it.
The scenes and plots appear as follows:
Force and
Pressure
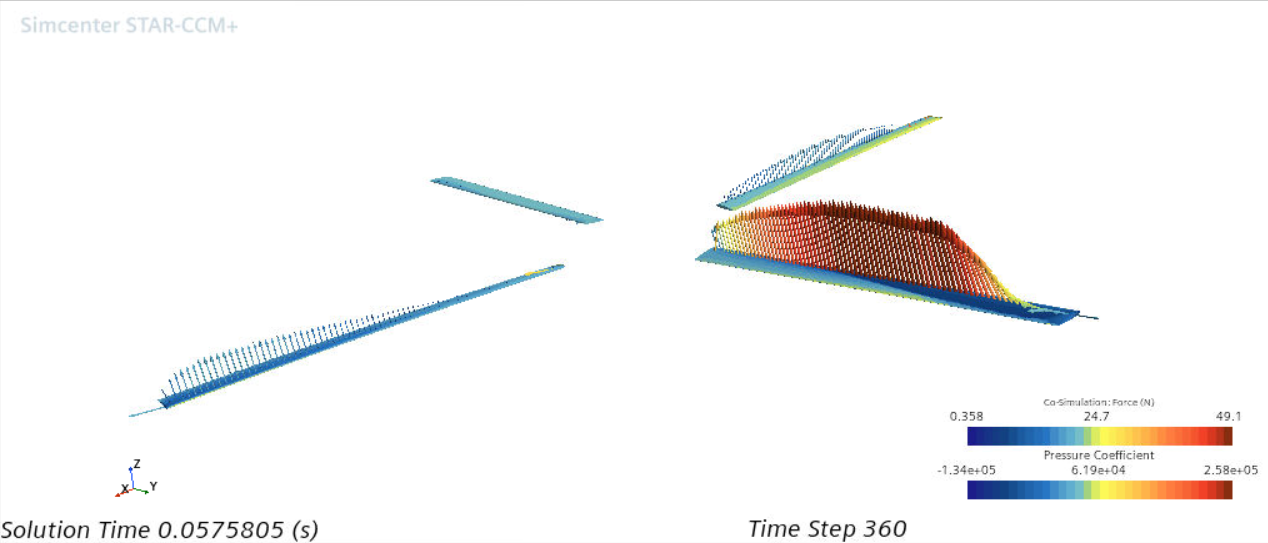
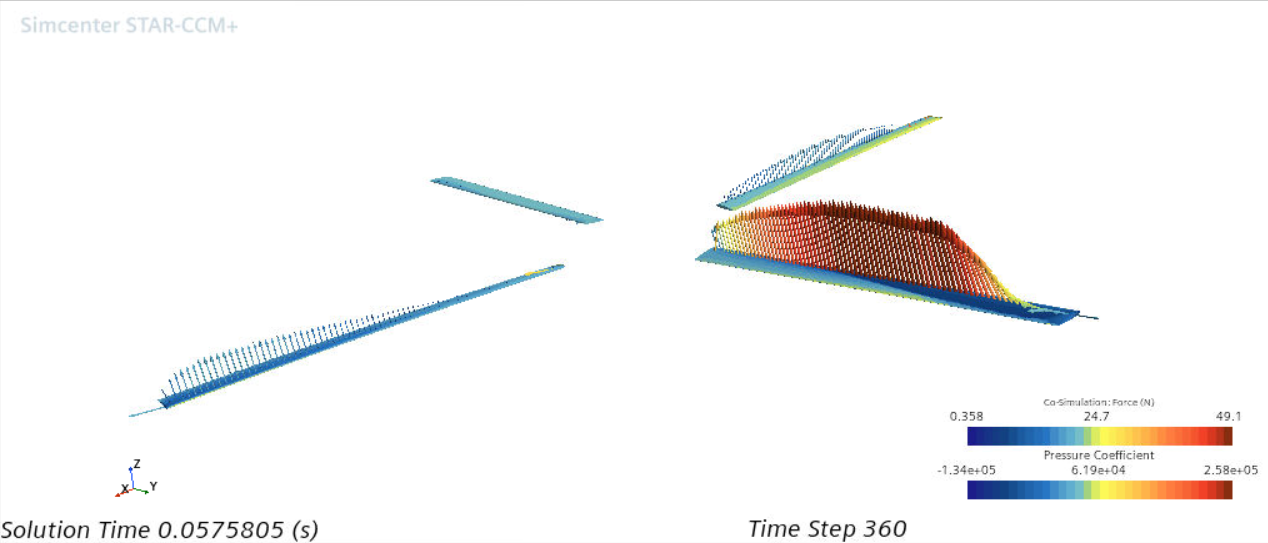
Rotor Force Monitor
Plot
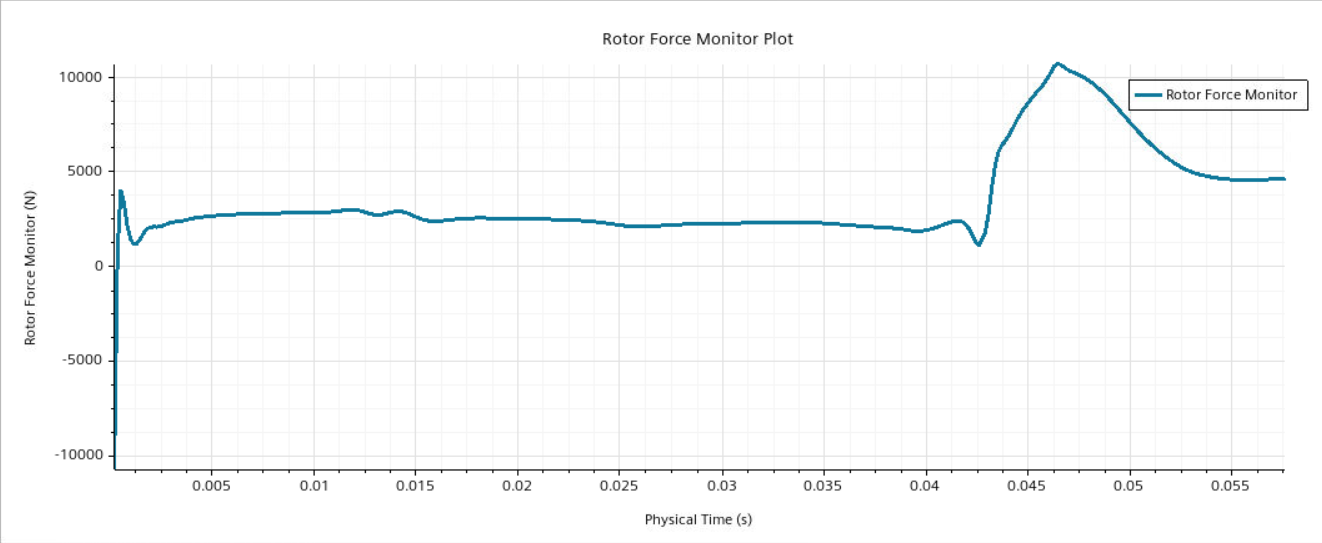
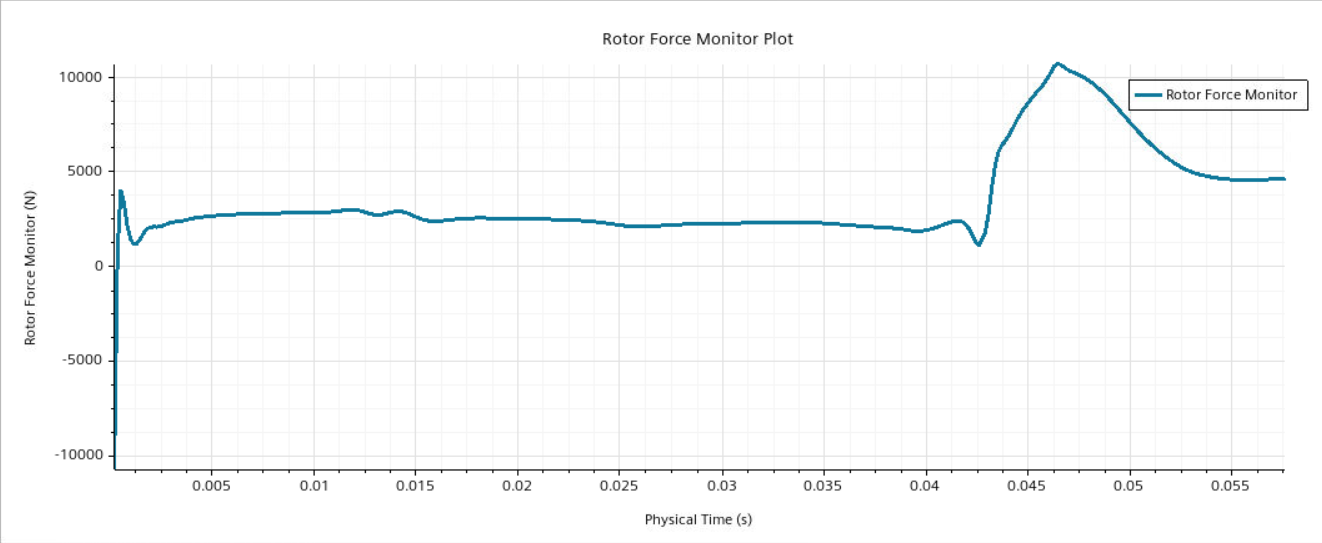
Blade 1 Force Monitor
Plot
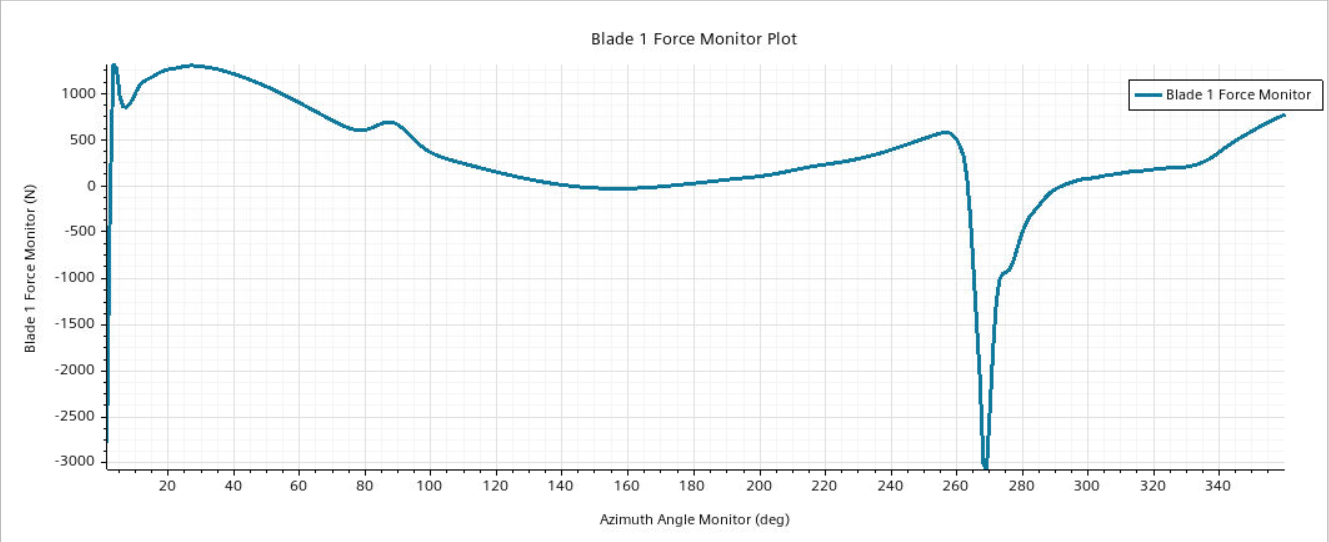
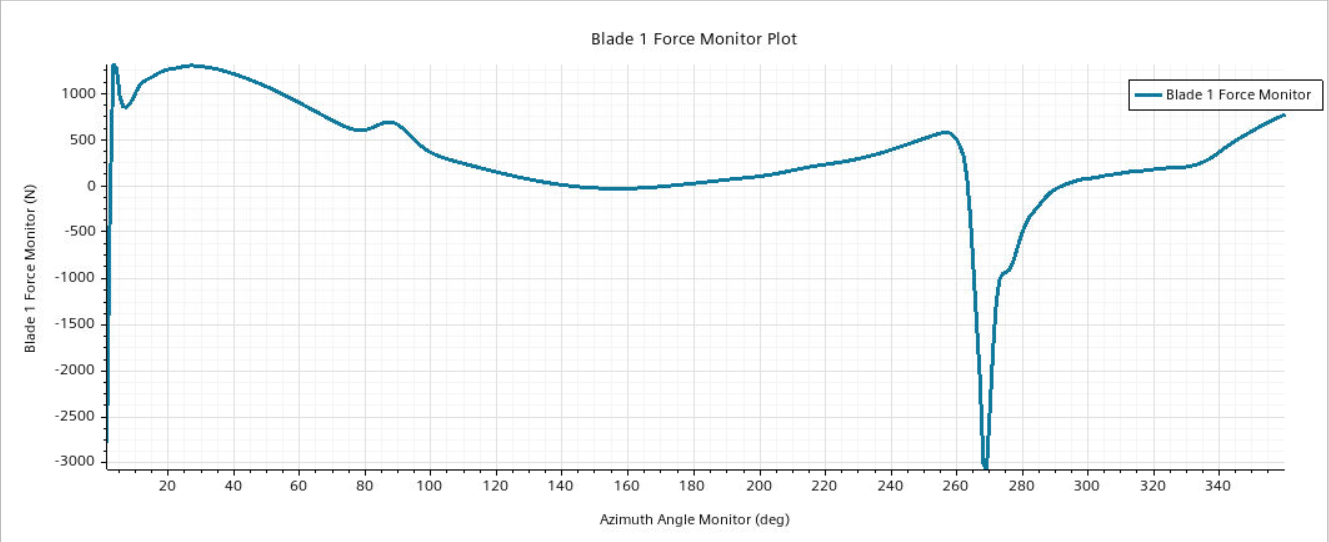
LE Displacement Monitor
Plot
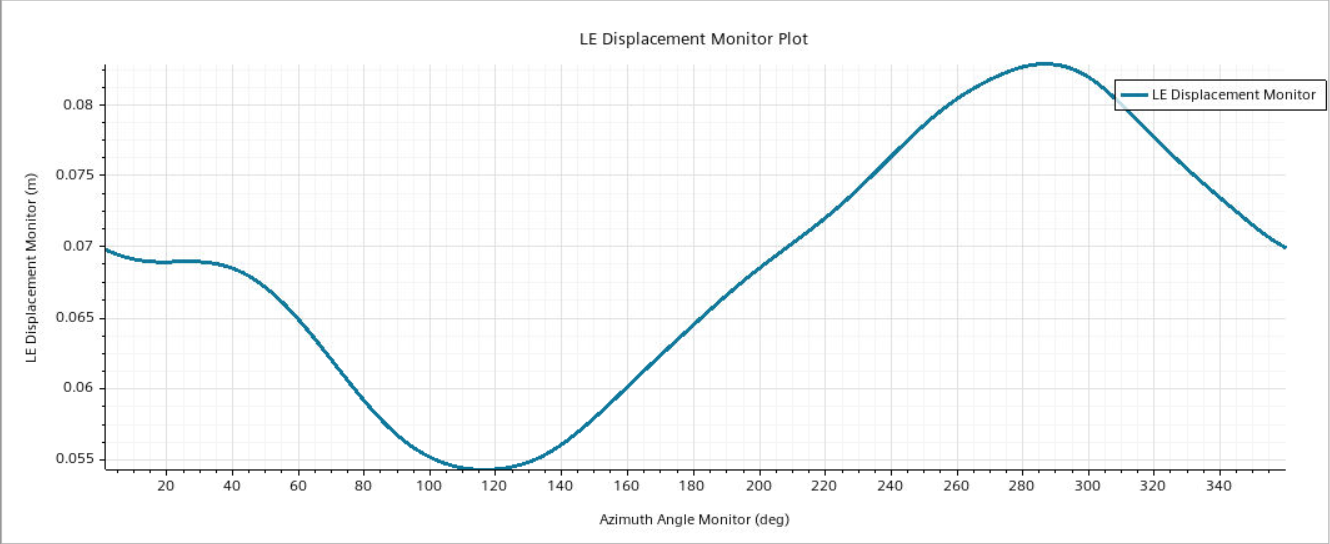
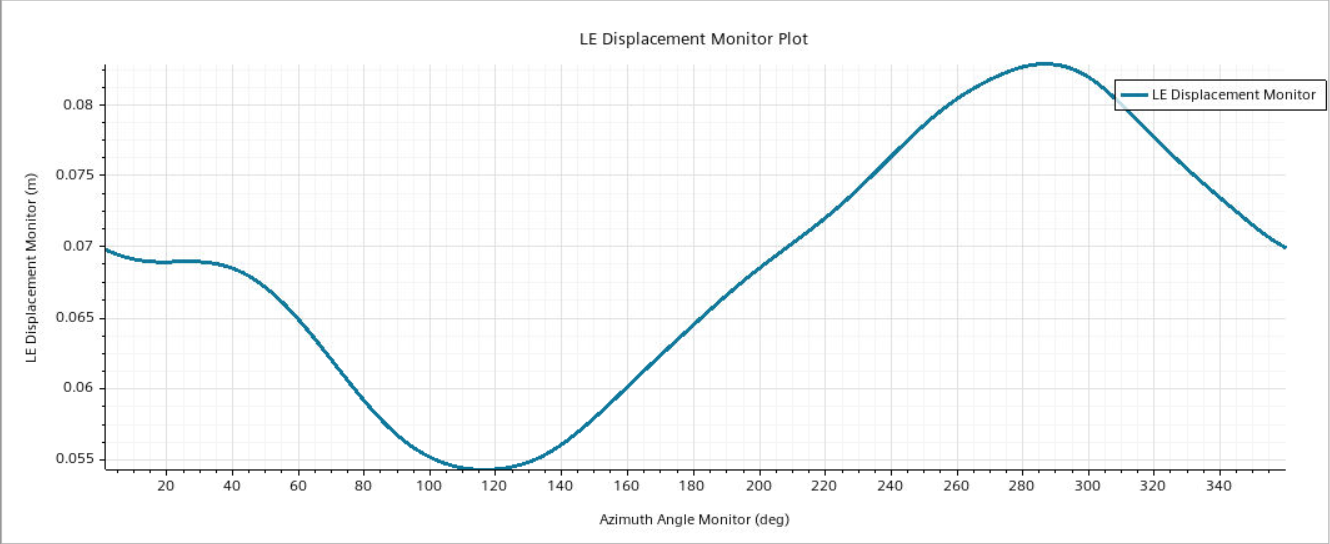
As you only run the simulation for one full rotation, it is likely the results are not converged. However, due to the large number of time-steps required, it can be computationally expensive and time consuming to obtain a converged rotor blade aeroelasticity study. Below are the plots after 5 rotations (1800 time-steps) for comparison:
Rotor Force Monitor
Plot
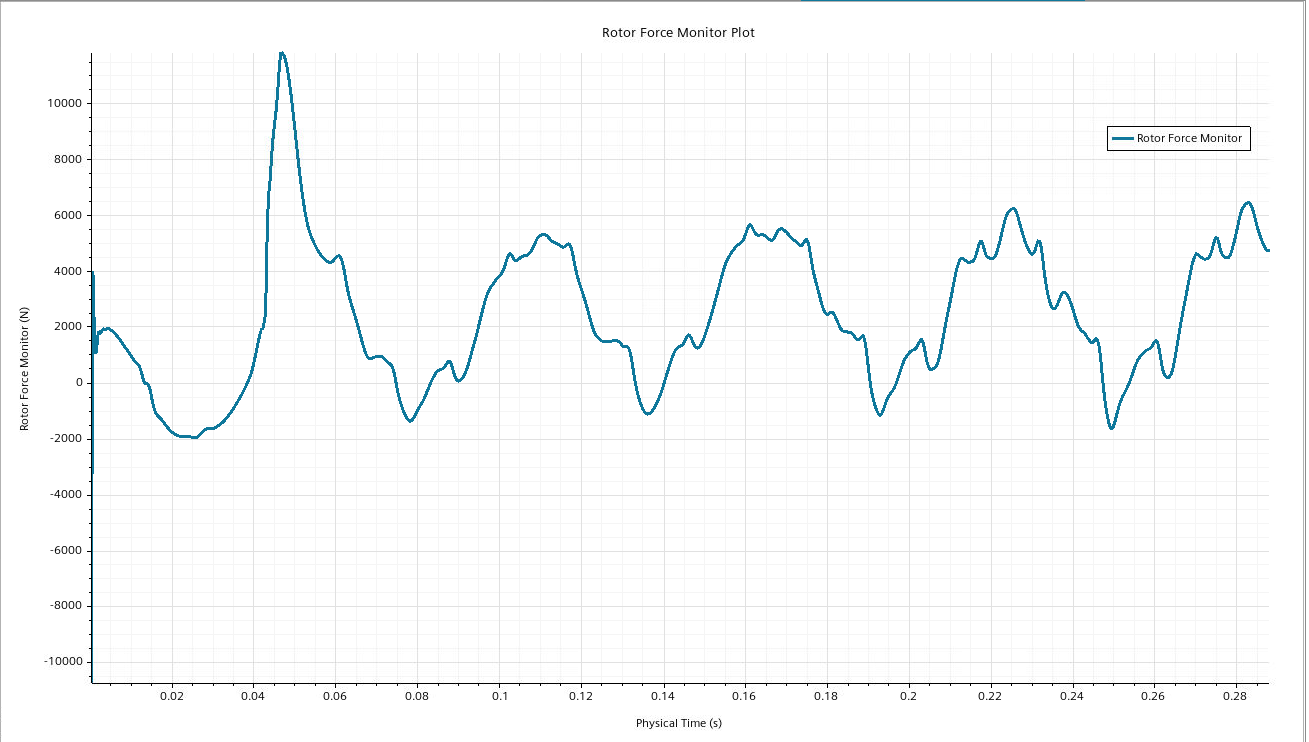
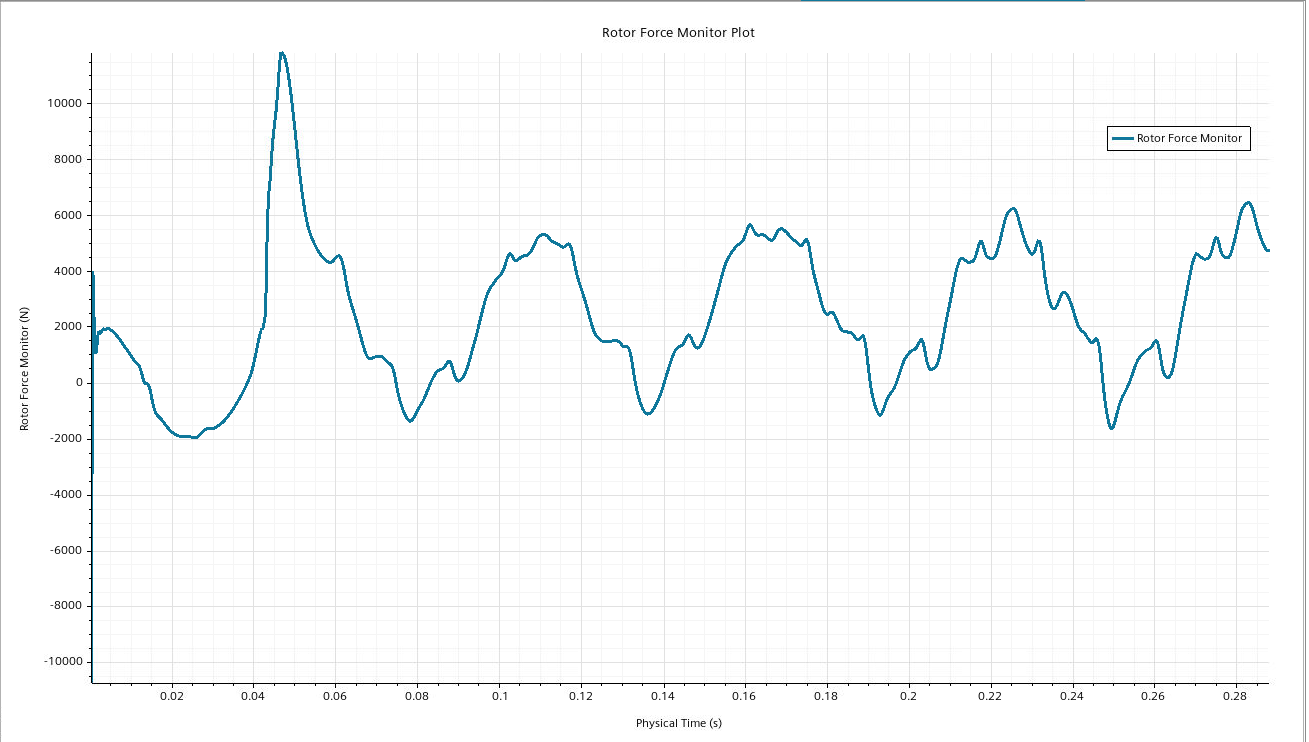
Blade 1 Force Monitor
Plot
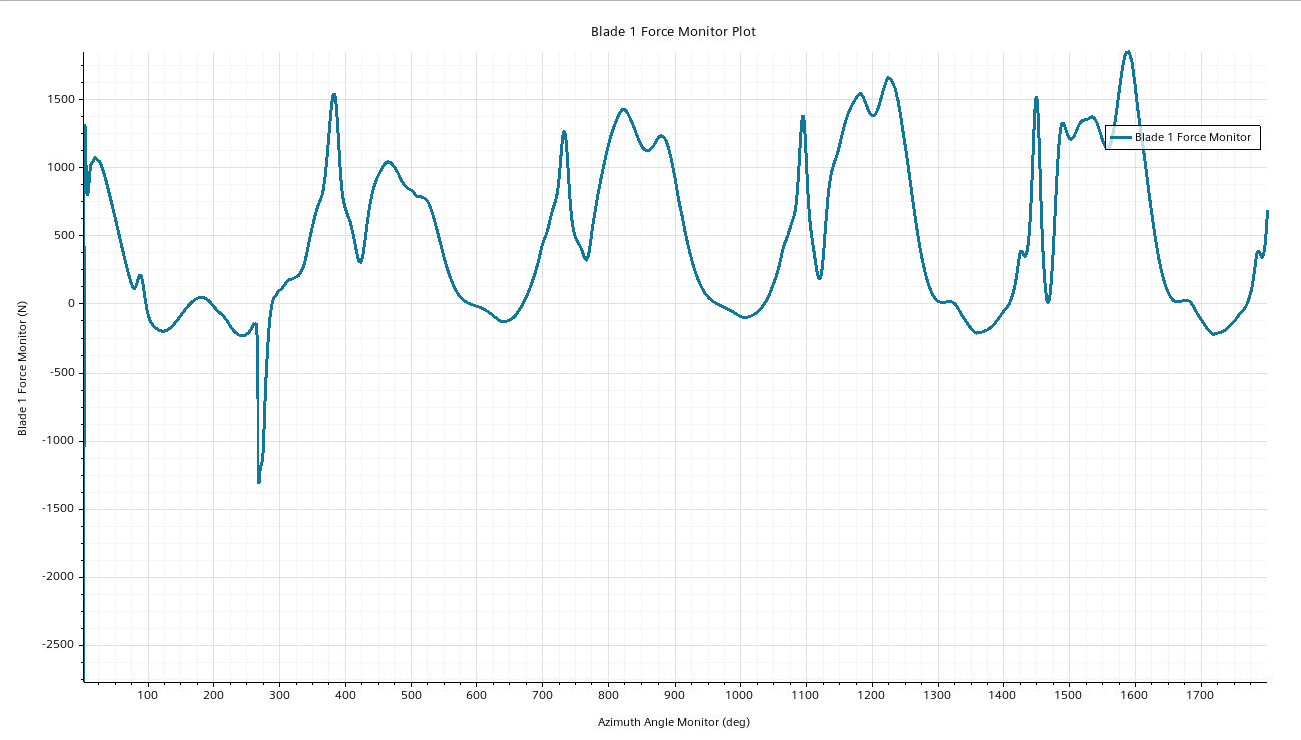
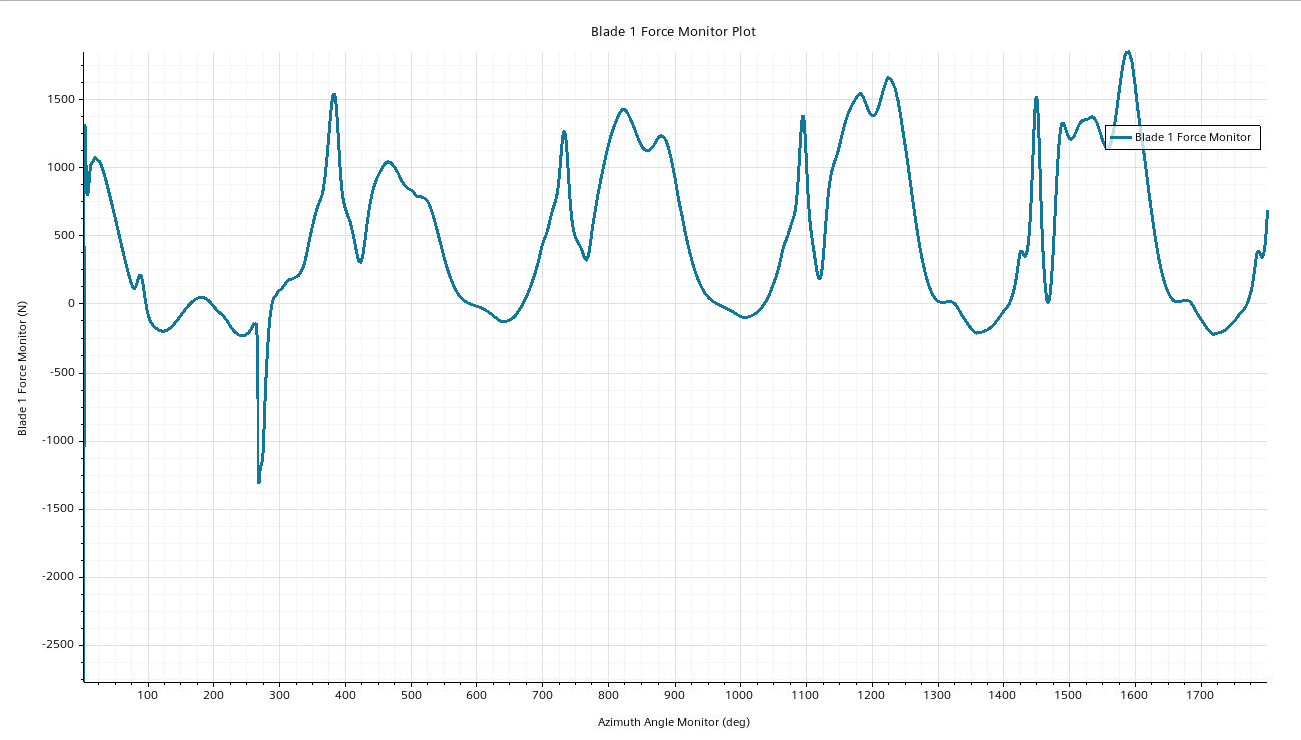
LE Displacement Monitor
Plot
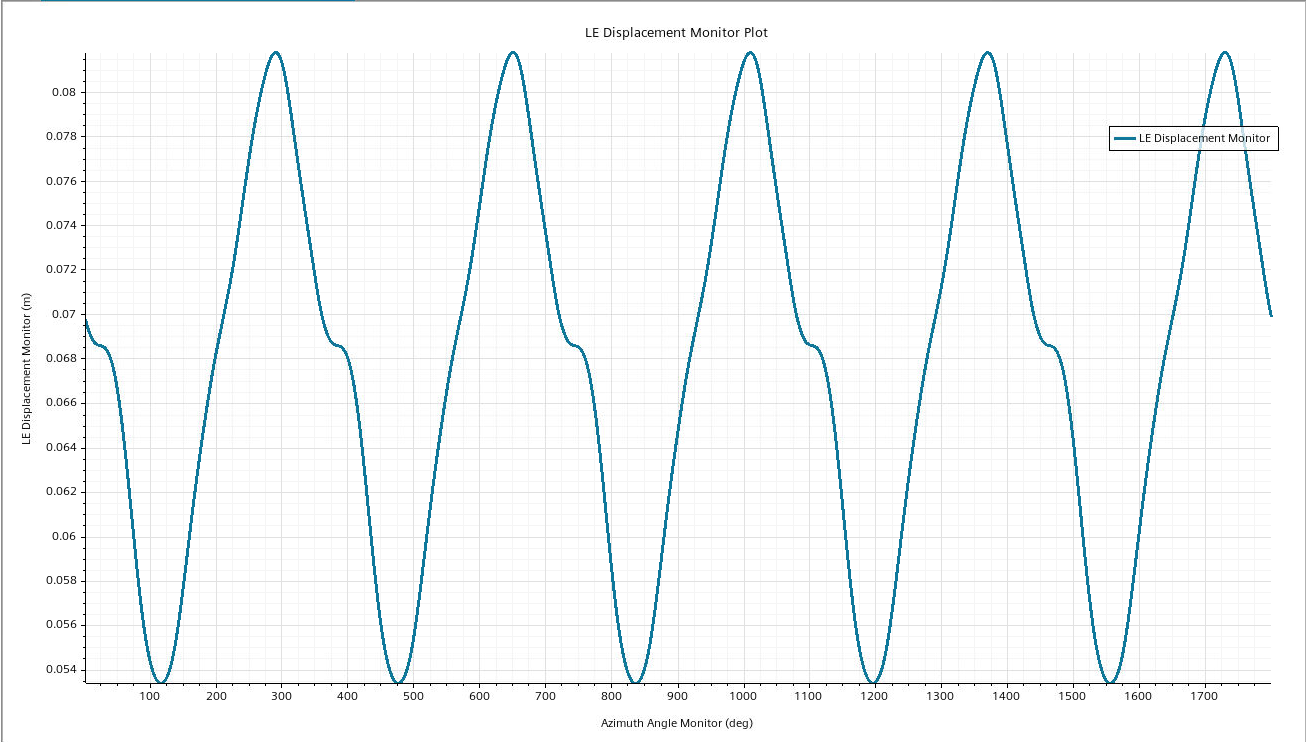
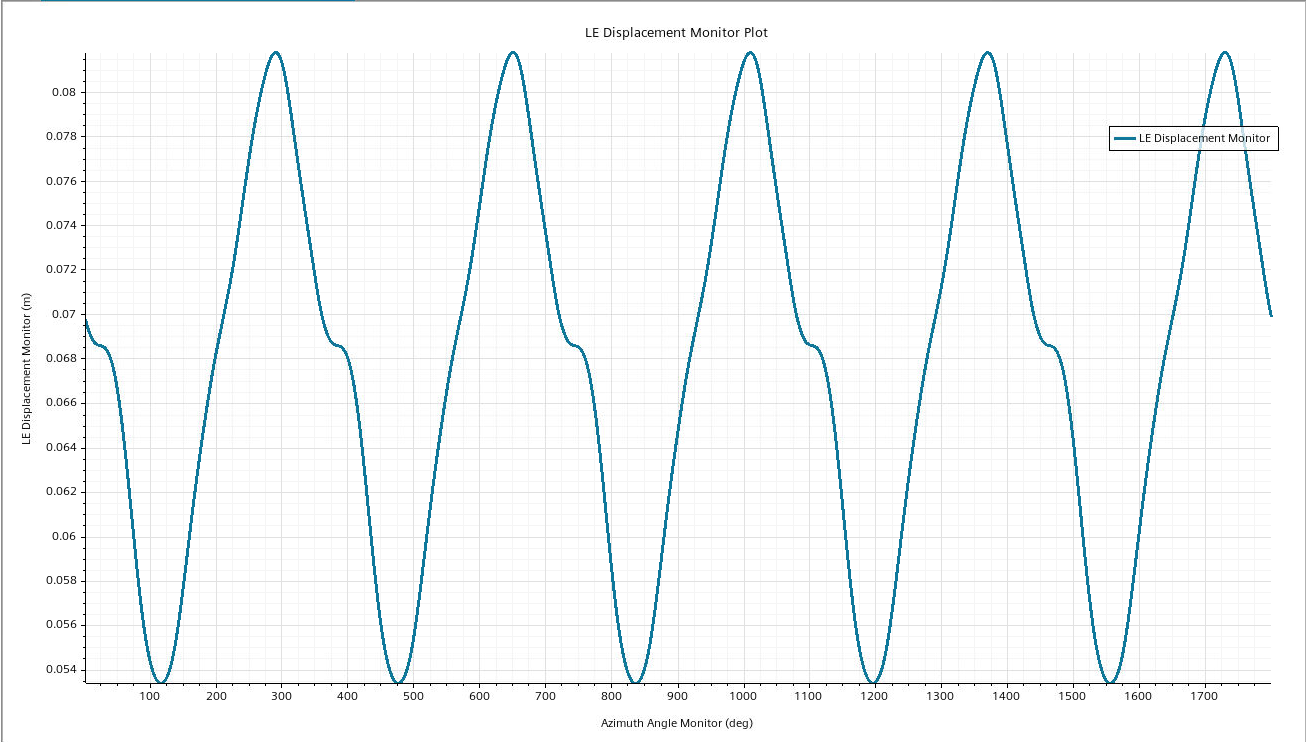